激光成形及修复技术通过高能激光束与材料的精密相互作用,实现高效精准的工业应用,其核心在于工艺优化、智能控制和多学科融合。以下是实现这一目标的关键路径及典型应用场景:
一、关键技术实现路径
1. 数字化工艺设计
模型驱动加工:基于CAD/CAM构建三维模型,通过仿真软件(如ANSYS)预测热应力分布,优化扫描路径与功率参数,减少变形。
材料数据库:建立金属粉末/丝材的熔凝特性数据库(如Ti6Al4V、Inconel 718),匹配最佳工艺窗口(如激光功率、扫描速度、搭接率)。
2. 高精度闭环控制系统
实时监测:集成红外热像仪、高速摄像机和熔池传感器,动态调整激光参数(如IPG光纤激光器的功率波动控制在±1%)。
自适应控制:采用AI算法(如深度强化学习)识别缺陷(如气孔、未熔合),即时修正工艺参数。
3. 复合制造技术
增减材一体化:结合激光沉积(LMD)与五轴铣削(如DMG MORI混合设备),实现近净成形与高表面精度(Ra<5μm)。
原位修复技术:在航空叶片修复中,通过激光熔覆+超声冲击强化,提升疲劳寿命至新件的90%以上。
4. 材料结构协同设计
梯度材料制备:通过多材料送粉系统(如双料斗送粉器)制造功能梯度部件(如火箭喷嘴的耐热/导热过渡层)。
微观组织调控:利用超快激光(皮秒/飞秒级)细化晶粒至亚微米级,提升钛合金修复区的抗蠕变性能。
二、典型工业应用场景
1. 航空发动机修复
案例:GE公司采用激光定向能量沉积(DED)修复高压涡轮叶片,材料利用率提升70%,成本降低50%相比传统替换。
精度指标:轮廓误差<0.1mm,热影响区深度<200μm。
2. 模具快速再制造
技术:选区激光熔化(SLM)修复汽车冲压模具刃口,硬度恢复至HRC 5862,周期缩短80%对比电镀工艺。
效率:局部修复区域加工速度达50100 cm3/h。
3. 大型构件现场维修
方案:便携式激光修复机器人(如TRUMPF TruLaser Cell 3000)在船舶甲板裂纹修复中,单道熔覆宽度38mm可调,抗拉强度达母材95%。
4. 精密医疗器械定制
创新:电子束熔融(EBM)与激光抛光联用制造骨科植入物,表面孔隙率<0.5%,实现骨细胞定向生长。
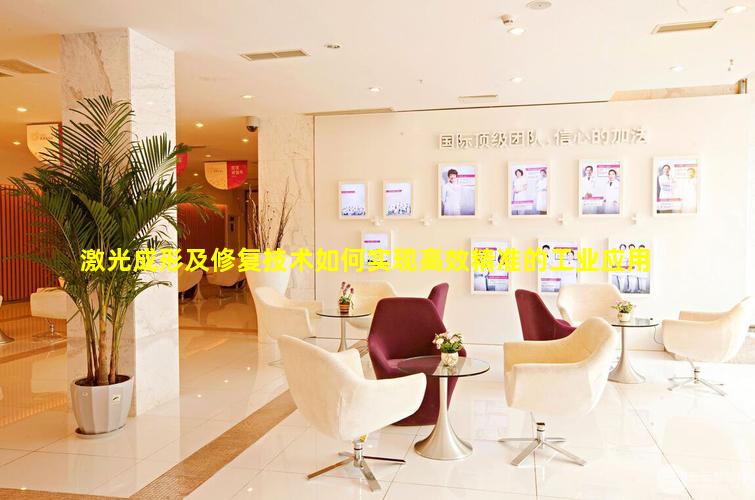
三、前沿发展方向
超快激光微纳制造:飞秒激光加工心血管支架,切割精度±2μm,边缘无热损伤。
数字孪生集成:西门子NX平台实现修复过程全生命周期模拟,预测残余应力误差<10MPa。
绿色制造:采用废粉回收系统(回收率>95%)与节能激光源(电光转换效率>40%)。
四、挑战与对策
残余应力控制:引入电磁场辅助激光加工,降低应力峰值30%50%。
多材料兼容性:开发通用型过渡层材料(如NiCrAlY合金)解决异种材料结合难题。
标准化缺失:推动ASTM/ISO制定激光修复验收标准(如ASTM F增材制造件缺陷评级)。
通过上述技术融合与场景适配,激光成形及修复技术正推动工业制造向“零缺陷、近净形、全生命周期”的智能化方向发展。