胶体磨骨泥流水线的高效连续生产需要从设备选型、工艺优化、自动化控制和系统管理等多方面进行综合设计。以下是实现高效连续生产的关键步骤和解决方案:
1. 原料预处理与连续供料
均匀供料系统
采用螺旋输送机、振动给料机或泵送系统,确保骨料(如动物骨骼)连续、稳定地进入生产线,避免间歇式供料导致的效率瓶颈。
预破碎与清洗
骨料先经粗破碎(如颚式破碎机)和高压清洗,去除杂质并减小粒径,提高后续胶体磨的处理效率。
2. 核心设备:胶体磨的高效配置
多级研磨串联
采用多台胶体磨串联(如粗磨+精磨),分阶段细化骨泥粒径(通常目标为2050μm)。例如:
一级胶体磨:快速破碎至μm;
二级胶体磨:精细研磨至目标细度。
设备参数优化
转子转速:根据骨料硬度调整(通常10,00020,000 rpm);
间隙控制:动态调节磨盘间距(如50200μm),平衡效率与能耗;
冷却系统:内置水冷或空冷,防止过热导致蛋白质变性。
3. 连续化工艺设计
封闭式管道连接
各设备间通过管道和泵(如螺杆泵、离心泵)无缝衔接,减少中间停滞和污染风险。
在线均质与混合
在研磨后增设高压均质机(2050 MPa),进一步均质化骨泥,同时可在线添加辅料(如调味剂、防腐剂)。
4. 自动化与智能控制
PLC/DCS控制系统
实时监测关键参数:温度(≤40℃)、细度(激光粒度仪)、流量(流量计);
自动调节:根据反馈动态优化研磨时间、转速和供料速度。
故障预警与自停
设置振动传感器和压力报警,异常时自动停机保护设备。
5. 后处理与包装
连续灭菌(如UHT或巴氏杀菌)
骨泥经管道式灭菌机(8595℃,1530秒)后直接进入无菌灌装线。
自动分装
采用伺服驱动的灌装机,配合重量/体积传感器,实现高速精准包装(如袋装、罐装)。
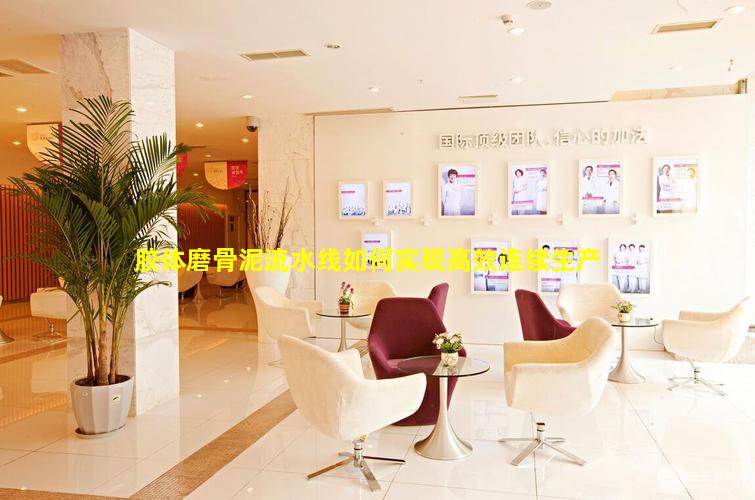
6. 节能与资源回收
热能回收
灭菌环节的余热用于预热原料,降低能耗。
废水处理闭环
清洗水经沉淀、过滤后循环使用,减少水耗。
7. 维护与效率保障
CIP(就地清洗)系统
定期自动清洗管道和胶体磨,避免交叉污染和堵塞。
预防性维护
定期更换磨盘、密封件,保持设备最佳状态。
案例参考
某肉类加工厂的骨泥生产线通过以下改进实现产能提升30%:
将单台胶体磨改为三级串联;
引入在线粒度检测自动反馈系统;
采用螺杆泵替代离心泵,解决骨泥高粘度输送问题。
关键成功因素
设备匹配性:胶体磨的耐磨材质(如碳化钨)和结构需适配骨料特性。
工艺连贯性:从原料到包装全程无断点设计。
数据驱动:通过SCADA系统收集生产数据,持续优化参数。
通过上述措施,胶体磨骨泥流水线可实现每小时数吨级的高效连续生产,同时保证产品品质稳定。