实现精密五轴联动激光整形技术的高效精准控制,需要从系统架构、运动控制算法、激光参数优化、误差补偿及智能化技术等多维度协同优化。以下是关键实现路径和技术要点:
1. 多轴协同运动控制
高动态响应伺服驱动
采用直线电机/力矩电机搭配高分辨率编码器(如纳米级光栅尺),确保各轴(X/Y/Z线性轴 + A/C旋转轴)的动态响应一致性,减小机械滞后。
插补算法优化
开发自适应NURBS(非均匀有理B样条)插补算法,解决传统线性插补在复杂曲面加工中的速度波动问题,提升轨迹平滑性。
实时前瞻控制(Lookahead)
通过预读多段加工路径,动态调整加速度和加加速度(Jerk),避免尖锐拐角处的振动和过冲。
2. 激光运动同步耦合
时间空间同步策略
利用FPGA硬件实现激光脉冲与轴位置的μs级同步(如PWM信号与编码器反馈的硬实时匹配),确保激光能量在动态运动中精准沉积。
光束指向补偿(Beam Steering)
通过振镜或声光调制器(AOM)实时校正激光焦点位置,补偿旋转轴引起的焦点偏移(如A/C轴旋转时的光程变化)。
3. 误差建模与补偿
全闭环反馈系统
融合光栅尺、激光干涉仪和视觉闭环反馈,构建基于卡尔曼滤波的多传感器数据融合系统,实时修正位置误差。
热变形补偿
建立主轴热伸长与导轨温升的有限元模型(FEM),通过温度传感器数据动态调整各轴零点偏置。
几何误差标定
采用球杆仪或激光跟踪仪进行21项几何误差(如垂直度、直线度)参数辨识,并写入控制器实现软件补偿。
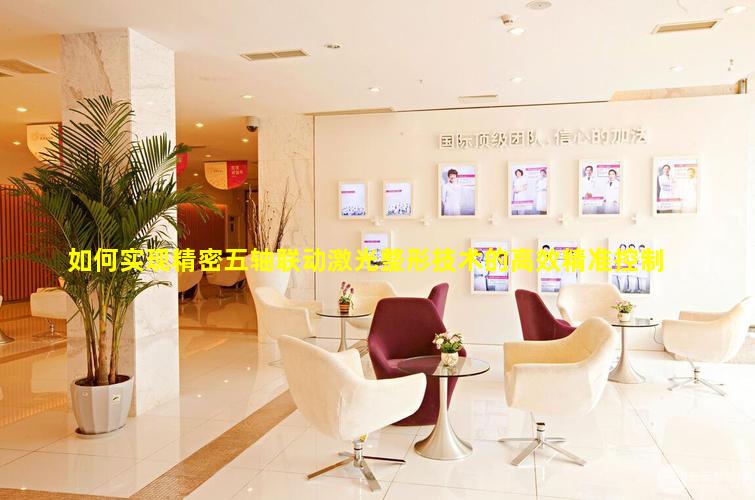
4. 智能参数优化
加工参数自适应
基于深度学习(如LSTM网络)建立激光功率、速度、焦点位置与表面粗糙度的映射关系,实时优化工艺窗口。
数字孪生仿真
在虚拟环境中预演加工过程,通过物理引擎(如ANSYS LSDYNA)模拟材料去除效应,生成最优刀轨后再执行。
5. 硬件平台选型
控制器:选用实时操作系统(如RTLinux)+ EtherCAT总线架构,控制周期≤100μs。
激光器:超短脉冲光纤激光器(如500fs脉宽),配合高速声光调制实现功率纳秒级切换。
五轴机构:摇篮式/双转台结构,重复定位精度≤±1μm,主轴径向跳动≤0.5μm。
6. 验证与标定方法
动态精度测试:通过加工标准螺旋微结构(如金字塔阵列),用白光干涉仪测量形貌误差。
带宽测试:施加正弦扫频激励,分析各轴幅频特性曲线,确保闭环带宽≥200Hz。
技术挑战与突破点
旋转轴动态误差:A/C轴在高速旋转时的离心变形需通过碳纤维轻量化设计降低惯量。
激光材料相互作用:针对不同材料(如碳化硅vs.铜合金)建立等离子体屏蔽效应模型,防止能量耦合不稳定。
通过上述技术整合,可实现纳米级面形精度(PV值<100nm)与毫米级深宽比结构的稳定加工,适用于光学自由曲面、涡轮叶片气膜孔等高端场景。实际案例显示,采用该方案可将传统五轴激光加工的轮廓误差降低60%以上,同时提升加工效率约35%。