激光叶片表面修复技术(Laser Cladding或Laser Surface Remanufacturing)在航空发动机维修与制造中的应用,确实具备显著提升耐久性的潜力,但其效果取决于技术实施的具体条件、材料特性以及工艺优化水平。以下是关键分析:
1. 技术原理与优势
精准修复与强化:
激光修复通过高能激光束熔化粉末或丝材,在叶片表面形成冶金结合的涂层,可修复磨损、腐蚀或裂纹,同时恢复几何精度。相比传统焊接,热影响区小,减少变形和残余应力。
材料性能提升:
可采用高温合金(如镍基合金)、陶瓷增强复合材料等高性能材料,显著提高叶片的抗高温氧化、耐腐蚀和抗疲劳性能。
延长寿命周期:
修复后的叶片性能接近甚至超过新品,减少更换频率,降低维护成本。
2. 对航空发动机耐久性的具体影响
抗疲劳性能:
激光修复可通过细化晶粒和引入残余压应力延缓裂纹萌生,但需严格控制工艺参数(如激光功率、扫描速度)以避免气孔或未熔合等缺陷。
高温稳定性:
涂层的高温抗氧化能力(如添加Al、Cr元素)可减缓热障涂层(TBC)的退化,适用于高压涡轮叶片等高温部件。
气动效率保持:
修复后表面光洁度和轮廓精度对气动性能至关重要,激光技术可通过后续抛光(如激光抛光)减少湍流损失。
3. 挑战与限制
工艺复杂性:
航空叶片多为单晶/定向凝固合金,修复需匹配基体晶体取向,否则可能引发再结晶或性能劣化。
质量控制要求:
需通过无损检测(如X射线、荧光渗透)确保无内部缺陷,并验证修复部件的疲劳寿命(需通过加速试验)。
成本效益平衡:
初期设备投入高,但长期看,修复成本可能仅为新件的30%~50%,适合高价值部件。
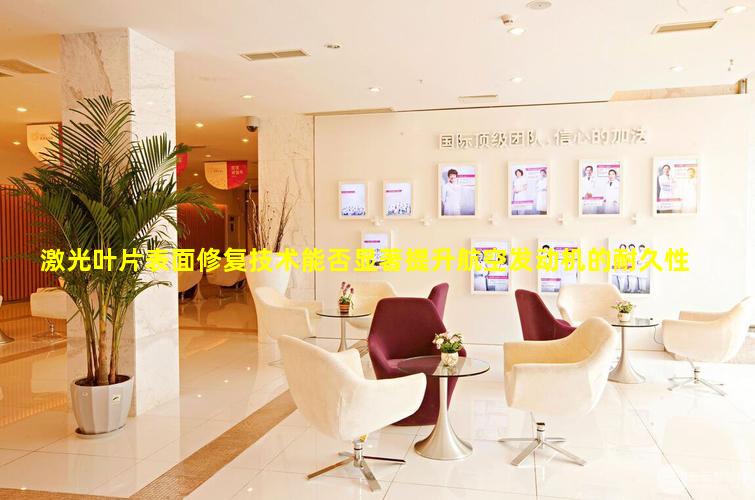
4. 实际应用案例
GE航空:采用激光修复高压涡轮叶片,延长服役周期20%以上。
罗尔斯·罗伊斯:将激光增材制造用于叶片修复,减少材料浪费并提升供应链韧性。
结论
激光叶片表面修复技术若能解决材料匹配性和工艺稳定性问题,可显著提升航空发动机的耐久性,尤其在高温部件修复和性能强化方面。其价值不仅体现在寿命延长,还在于降低全生命周期成本和环境足迹。未来随着智能监控(如数字孪生优化参数)和新型材料(如纳米涂层)的发展,该技术的潜力将进一步释放。